The design of high temperature valves
Posted: 12/20/2018 17:12:42 Hits: 88
In recent decades, with the development of modern science and technology, there is an increasing demand for high temperature valves in engineering projects, among petrochemical, chemical, electric power and other industries. Since long-term high-temperature environment will affect the physical properties and mechanical properties of metal materials, it is necessary to pay attention to the influence of high temperature on related factors when designing and selecting high-temperature valves.
The definition and classification of high temperature valves
In general, a valve whose operating temperature is higher than 450 ℃ is called a high temperature valve. There is no uniform standard for the classification of high temperature grades for this kind of valves right now. In one standard, the operating temperature grades are divided in 425-550 ℃, 550-650 ℃, 650-730 ℃, 730-816 ℃ and above 816 ℃, which defines that in 425-816 ℃, the valves mainly rely on the selection of suitable materials to ensure their performance, and for situation where the temperature is above 816 ℃, it is more important to adopt special design methods, such as insulated lining or taking cooling measures. In another standard, the ultra-high temperature pneumatic angle globe valve has five sets of cooling structure to ensure that the valve can work fine at a temperature of 2000 ℃.
Commonly used high temperature valves
High temperature valves include high temperature gate valves, high temperature check valves, high temperature ball valves, high temperature butterfly valves, high temperature needle valves, high temperature throttle valves, high temperature relief valves, etc. Among them, gate valves, globe valves, check valves, ball valves and butterfly valves are more commonly used.
Design points for high temperature valves
When designing high temperature valves, pay special attention to the effect of thermal expansion, thermal alteration and mechanical properties of the material. Due to the difference in thermal expansion coefficient of the material and the heat load on the part, even if the valve seat and the valve core are heated at almost the same time, they will have different properties, like the expansion amount at high temperature. In order to effectively reduce jam or rubbing between parts caused by temperature, the working gap between the valve parts should be increased according to the thermal expansion coefficient, stress, the actual temperature. Heat exchanging process at high temperature will cause loose connection between the valve seat and the guide sleeve, accelerating aging of the parts. So when designing, corresponding measures should be taken according to the specific conditions. For example, the priority in designing for sealing structure is to adopt resilient seats. High temperature will significantly affect the mechanical properties of the material. The strength, hardness, plasticity, elastic modulus, etc. of the material will be different at different temperatures. The influence of these factors on the valve performance should be fully considered in the design.
The selection of high temperature valve material
When designing high temperature valves, it should be noted that the temperature must not exceed the maximum allowable temperature of the material. Factors such as the corrosiveness of the medium and the stress level should be considered as well.
Carbon steel and alloy steel pipes are prone to cause hydrogen embrittlement under certain conditions. Depending on the source of hydrogen in the metal, hydrogen embrittlement, which usually refers to hydrogen attack, is related to temperature, pressure and the solubility of hydrogen in steel, and often divided into internal hydrogen embrittlement, electrochemical hydrogen embrittlement and environmental hydrogen embrittlement.
The material selection considering the hydrogen working condition should be based on the maximum operating temperature plus a margin of 20-40 ℃, and the partial pressure of hydrogen in the media. Cr-Mo steel is often used in high temperature situation. In addition, since austenitic stainless steel does not decarburize under any temperature conditions or hydrogen partial pressure, it can also be used in this situation, but the cost of this material need to be considered.
Hydrogen sulfide corrosion conditions often occur in petrochemical projects. So normal valves cannot meet the safety production requirements. According to an analysis from experts, when the temperature is equal or less than 120 ℃ and water exists, stress corrosion cracking of steel is easy to happen; corrosion won't occur when the temperature is equal or less than 240 ℃ and there is no water; when the temperature is higher than 240 ℃, the steel may be rapidly and evenly corroded. The environment with hydrogen and hydrogen sulfide will accelerate the corrosion rate.
In other corrosive conditions, the materials of high temperature valves, such as stainless steel, nickel-based alloy, titanium alloy can be selected according to the medium and temperature, etc.
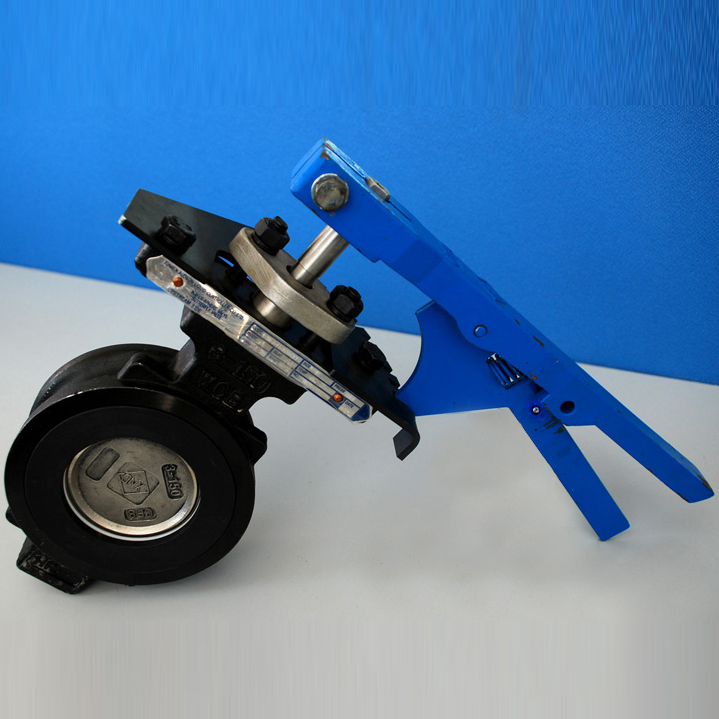