Eight factors that must take into account in purchase of valves
Posted: 12/22/2018 17:04:43 Hits: 53
General requirements
1. The specifications and categories of valves should comply with the requirements of the piping design.
2. The model number of valves should indicate the requirement of the standard number. The relevant description of the model number should be indicated if the valve follows the enterprise standard.
3. The working pressure of the valves should not be higher than the requirement. Under the premise of not affecting the price, the working pressure of the valve should be greater than the actual working pressure of the pipeline. Any side of the valve should be without leakage and able to withstand 1.1 times the working pressure of the valve when closing. The valve body should be able to withstand twice the valve pressure requirement when it is open.
4. The valve manufacturing standard should state the national standard number on which the instrument is based. If it is an enterprise standard, the enterprise contract should be attached to the purchase contract.
The quality of valves
1. The main body materials should be ductile iron, and the actual data of physical and chemical test should be indicated.
2. It is better to use stainless steel stem (20Cr13). And large-diameter valve should also use stainless steel stem.
3. Cast aluminum brass or cast aluminum bronze are used for screws, and the hardness and strength of them are greater than those of the valve stem.
4. The hardness and strength of valve stem bush materials should not be greater than those of the valve stem, and do not form electrochemical corrosion with the valve stem and valve body under water immersion conditions.
The materials of the sealing surface
1. Different types of valves have different requirements for the sealing methods and materials.
2. The materials, fixing methods and grinding methods of the copper ring of normal wedge gate valves should be in detail.
3. Physical and chemical testing data of soft sealing gate valves
4. Butterfly valves should indicate the material of the sealing surface on the valve body and that on the butterfly plate; their physical and chemical testing data, especially the hygienic requirements of rubber, anti-aging performance, wear resistance; nitrile rubber and EPDM rubber are usually used in butterfly valves. It is forbidden to use recycled rubber.
Valve shaft packing
1. Due to the opening and closing of valves in the pipe network are not frequent, the sealing effect of the packing should be able to maintain for a long time.
2. The valve shaft packing should also be in good condition when it is subjected to frequent opening and closing.
3. In view of the above requirements, the valve shaft packing should be able to not be replaced for life or more than ten years.
4. If the packing needs to be replaced, the design of valves should consider measures for situations where valves have to be replaced under water pressure.
Gearbox
1. The materials of the gearbox, the internal and external anti-corrosion requirements are consistent with the principle of the valve body.
2. The gearbox should have sealing measures, so it can be immersed under the condition of three-meter water column after assembly.
3. The opening and closing position limiting device on the gearbox, as well as the adjusting screws should be inside the box or outside the box, but special tools are required for work.
4. The design of the transmission structure should be reasonable. When opening and closing, the valve shaft can only be rotated, so that it does not move up or down.
5. The gearbox and the valve shaft seals should not be connected as a leak-free whole, unless there are reliable anti-leakage measures.
6. There should be no debris in the box and the meshing parts should be protected by lubricating grease.
Valve operating mechanism
1. The opening and closing direction of the valve should be closed clockwise.
2. Due to the valves in the pipe network are often manually opened and closed, the number of opening and closing rotations should not be too much, the large diameter valves should also be within 200-600 times.
3. In order to facilitate manual opening and closing, the maximum opening and closing torque should be 240N.m under pipeline pressure.
4. The valve opening and closing operation end shall be square and standardized in size and facing the ground so that one can operate directly from the ground. Valves with discs are not suitable for the underground pipe network.
5. The scale line of the degree of opening and closing of the valve should be cast on the cover of the gearbox or the outer cover of the display panel after changing the direction, which should face the ground and coated with phosphor. If the management of the disc pointer is good, use stainless steel plates, otherwise the material should be painted steel plate. Do not use aluminum sheets.
6. If the valve is buried deeply, the operating mechanism and display panel are not less than 1.5m away from the ground, the extension rod should be fixed firmly so that the operator can observe and operate from the ground. That is to say, the opening and closing operation of valves in the pipe network is not suitable for down-hole operation.
Performance testing of valves
1. When a certain specification of valves is manufactured in batches, an authoritative organization shall be entrusted to perform the following performance tests: the opening and closing torque of the valve under the working pressure; the times of opening and tight closing under working pressure; the detection of the flow resistance coefficient of the valve in pipeline water delivery.
2. The valves should be tested as follows before leaving the factory: When the valve is open, the valve body should be subjected to a detection with double valve pressure value; When the valve is closed, its two sides should withstand 1.1 times the valve working pressure value without leakage, but the leakage value of metal sealed butterfly valves should not greater than the relevant requirements.
Corrosion protection
1. The inside and outside of valve body, including gearbox body, should firstly be derusted by shot blasting, and cover with electrostatically spraying powdered non-toxic epoxy resin with more than 0.3mm thickness.
2. The interior of the valve body and the various parts of the valve plate are required to be fully anti-corrosive. One the one hand, they will not rust when immersed in water, and no electrochemical corrosion will occur between metals. On the other hand, the smooth surface will reduce the water resistance.
3. The hygienic requirements for epoxy resin or painting for corrosion protection in the valve body should be tested by the relevant authority. Chemical and physical properties should also meet the relevant requirements.
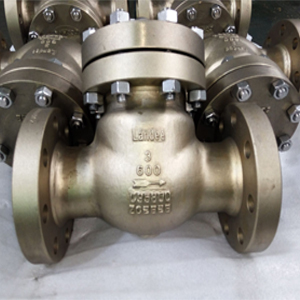